Bagan, etc.
July, 2004
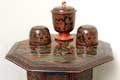 |
Lacquerware
|
|
|
 |
Lacquerware
The production of lacquerware has been a tradition in the Bagan area since the time of the Bagan Empire. Today it is still the largest industry (outside of agriculture) in the region. We visited a lacquerware shop in Bagan Myothit (New Bagan) and watched them making modern lacquerware. First, a framework is made of bamboo strips, woven much like a basket. This will support the lacquer. The finer the materials used, the thinner and more flexible the bowl. The best quality bowls substitute horse hair for some of the bamboo.
Next, the framework is coated with a thin layer of lacquer. The thinner each layer, and the more of them, the higher the quality of the finished product. The lacquer is really just a very thick paint. After each coat is applied, the piece must be kept in a cool cellar to cure before the next coat is applied. It can take months for a good piece to be completed.
Once completed, the piece is decorated, usually with several colors. First, a pattern for one color is stenciled onto the surface. Next, the pattern is incised into the surface, one color at a time. After the incisions are complete, colored lacquer is applied to fill the recesses and then allowed to cure. Then the second color is stenciled, incised, and filled. The whole process is lengthy and labor intensive.
Here is an example of a finished bowl. Made of thin bamboo and horsehair, it is of the highest quality. Jamie is squeezing it to demonstrate its flexibility. We purchased a small set of these bowls and a low table (see the photo at left). Although you can buy poor quality lacquerware from the touts at the temples for less money, we felt it was worth it to pay for the higher quality. The plain bowls cost us about $5.00 each; total cost for three bowls and the table was $47.00. We think we got a bargain.
|
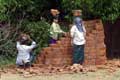 |
Carrying brick
|
|
|
 |
Terra cota brick
Brickmaking techniques are essentially the same throughout the world. The manual techniques we saw in Bagan probably haven't changed for thousands of years. The process begins with a source of clay. In Bagan, the bricks are made right where the clay is found. Next, the clay is mixed with water and frit (probably sand or broken brick), then kneaded to provide an even mix.
The wet clay is first pushed into a metal mold and then turned out onto a thin piece of wood, which is used to support the wet brick. The wet bricks are placed on edge, close to one another for support, to dry. Once they have dried enough to support themselves, they are restacked to allow air to circulate and speed the drying process. If it rains, the bricks must be covered to prevent damage.
Once the bricks are sufficiently dry, they are fired. No kiln is used. Firewood is simply stacked up between the rows of bricks, and burned. The fired bricks are used all around Bagan for new construction (see the photo at left) and for rebuilding the damaged archaeological sites.
The workers are paid by the owner of the land for each finished brick. Although these people were working at great speed, they produced only a few bricks a minute. Given the number of workers involved, and the low value of the completed bricks, they earn a very small income.
|
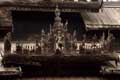 |
Monastery roof
|
|
|
 |
Nyaung U Monastery
We visited an out-of-the-way monastery in Nyaung U, the village that is closest to the archaeological site at Bagan. The monastery is in full operation, housing the monks and their novices. The building is built entirely from teak and is about a century old. It is in marvelous condition. The roof is beautifully decorated with intricate carvings that have remained sharp despite the years of sun and rain. (See also the photo at left.) Inside the monastery, one of the young monks showed us the chests where they store religious texts written in an ancient language that few people can still read.
|
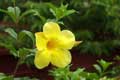 |
Flower
|
|
Index
|
 |
Miscellaneous
Finally, here are some last photos from Bagan. They include flowers, monks, and people at work. We hope you enjoy them:
return to the 2004 Journal Archive
|
|