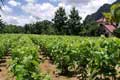 |
1. Mulberry trees
|
|
 |
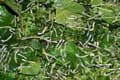 |
2. Silkworms
|
|
 |
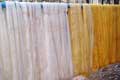 |
3. Clean silk
|
|
 |
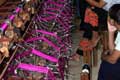 |
4. Dyed silk
|
|
 |
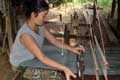 |
5. Weaving
|
|
|
 |
|
 |
Silk is produced by the larvae of the silkworm moth (bombyx). The silkworm is totally domesticated, and lives exclusively on mulberry leaves. When the mulberry trees are large enough, they are pruned to a good working height (see photo #1, at left). The mulberry leaves are hand picked each morning and processed for feeding to the silkworm larvae. When the larvae are very small, they cannot easily eat whole leaves. The leaves must be chopped very finely to make them suitable. As the larvae mature, they can be fed whole leaves, even whole branches.
The domesticated silkworms (photo #2) are very delicate and can only live in a carefully controlled environment. The silkworm house is specially designed to protect the silkworms from changes in temperature and humidity, and to keep out other insects. Large wooden trays are prepared to hold the mulberry leaves and silkworms while the larvae are eating and growing. They do nothing else during their whole lifetime. It takes 30-45 days for the silkworm larvae to mature. Each mature silkworm produces a single silk cocoon. The process can only be repeated about 4-6 times in a year, as production must stop during the rainy season. There are two species of native silkworms. One produces a cream colored silk, the other makes bright yellow silk.
Once the cocoons are formed, the silk must be unwound. Hot water is used to kill the larvae and loosen the silk fibers, allowing the silk to be collected. Each cocoon produces a single silk fiber about 800 - 1,000 meters long. Depending on the thickness of the fiber, 30 to 50 fibers are wound together to produce a silk thread. The whole process is done by hand using simple machines. The silk yarn must then be cleaned, being sure that all extraneous material is removed. To soften and brighten the silk, it is boiled in a caustic solution. This solution is obtained by soaking rice straw ash in water. In the past, when silk was being made for the King of Laos, they burned a special grass to obtain the ashes for this process. The cleaned silk (photo #3) is rinsed and dried, and is ready for dying.
Natural dyes are made from teak leaves, indigo, pandanas, and other local plants. Each produces its own distinctive color, and each dye can produce a range of tones. Some dyes are used cold, others must be boiling hot. This photo shows silk yarn and finished silk scarves that have been dyed with indigo dye. Synthetic dyes, which produce much brighter colors (photo #4), are also used.
Producing natural dyes begins with the appropriate plant material. For example, leaves from teak trees are pounded to release the sap, which produces a reddish colored dye. The pounded leaves are soaked in hot water so that the dye is taken up by the water. The silk is then soaked in the dye-water to transfer the color to the fabric or yarn. It takes a great deal of squeezing to work the dye into the fabric evenly and completely. The final step is to set the dye with a mordant to keep it from running. In the case of the teak leaf dye, this is done with lime juice. The acid in the limes lowers the pH of the dye, changing it a precipitate which is insoluble and will not wash out of the fabric.
The weaving is done by women. The looms are often simple machines, built by local carpenters. Many women prefer to weave at home (photo #5) where they can care for their families and avoid traveling to work. Others work in small workshops. The looms vary in design and complexity, depending on the materials being produced. Here are photos of looms being used to produce more complicated fabrics. The simplest looms are attached to the weaver using a backstrap. She controls the tension on the threads by leaning back against the backstrap. The finished product can be quite beautiful.
return to the 2004 Journal Archive
|