Native House Construction
November, 2002
The traditional Filipino house, at least in Bohol Province, is made entirely from plant materials. It is rapidly disappearing as modern construction materials based on concrete and steel have become more popular. Jim set out to learn how the old houses were built.
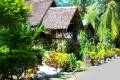 |
1. Native style house (91k)
|
|
 |
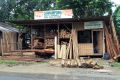 |
2. Lumberyard (88k)
|
|
|
|
Construction Overview
Native style houses (see thumbnail photo #1, at left) are constructed from just a few local plant materials. The most important of these are derived from the coconut palm, nipa palm, and bamboo. The basic structure is a post and beam framework built mostly with coco lumber, although other, more rot-resistant, woods are often used for the posts. The floors are made of split bamboo, the walls are covered with amakan, also made from split bamboo, and the roof is "shingled" with nipa palm fronds. The windows are often a simple lattice of widely spaced split bamboo. Many parts of the house are lashed together using tough fibers from other plants. The finished materials are sold at lumberyards (photo #2) that specialize in traditional products.
The completed house is cool, dry, and airy. It is also infested with insects, rats, lizards, snakes, and any other animal that wants to enter. And the materials are ephemeral, rotting quickly in this hot, humid climate. The houses require a considerable amount of maintenance, and must eventually be pulled down and rebuilt. The houses are also insecure, as one can easily kick a hole through the walls or windows. For all these reasons, the native houses are no longer popular. Anyone who can afford to do so now builds with concrete walls and steel roofing.
|
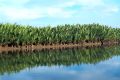 |
3. Nipa plantation (57k)
|
|
 |
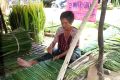 |
4. Nipa shingle construction (80k)
|
|
 |
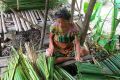 |
5. Nipa sewing (93k) |
|
|
|
Nipa Roofing
The traditional roofing material is made from the fronds of the nipa palm. The nipa plants are grown in mangroves, muddy areas along the rivers that flood with each high tide (photo #3). The plants are periodically pruned, removing the outer fronds while leaving the inner fronds to continue the process.
Next, the "leaves" are removed from the fronds and sold to the nipa shingle makers, who can be found all along the main road as it passes the Abatan River. You can see the leaves bundled up in the background in (photo #4). The leaves are folded over a small bamboo stick and then sewn on with a tough plant fiber (photo #5). It takes about 1-2 minutes to produce each shingle (there was some disagreement among the ladies about the time required). They sell the shingles for 130 pesos (about US$ 2.60) per 100 pieces. These ladies are entrepreneurs; they buy the materials, pay rent on the little building where they work, and sell the finished product to the customer. They make a living.
The nipa shingles are lashed onto the roof of the house by a builder working from the underside of the roof. The finished roof is not strong enough to support someone walking on it. Each shingle overlaps the one below it, with about 2" between rows of shingles. To save money, the shingles can be spaced further apart, but the life of the roof is reduced. A nipa roof can last up to 5-10 years before it must be replaced, but they often begin to leak in just a few years.
|
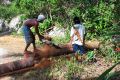 |
9. The lumber mill (114k)
|
|
|
|
Coco Lumber
The final important material for construction of the native house is coco lumber. Because of the way the houses are constructed, precise lumber sizes are not required. So the coconut trees are felled and milled by men using chain saws freehand (photo #9). The finished lumber is surprisingly consistent when one considers the way it is produced.
return to the 2002 Journal Archive
|
|